Insights into Energy - Saving Methods and Techniques for Centrifugal Pumps
Insights into Energy - Saving Methods and Techniques for Centrifugal Pumps
Centrifugal pumps are widely utilized in various industries, from water treatment plants to chemical processing facilities, playing a crucial role in fluid transportation. However, they are also significant energy consumers. In the pursuit of sustainable development and cost - effectiveness, understanding and implementing energy - saving methods for centrifugal pumps have become increasingly important.
One of the most fundamental ways to achieve energy savings is through proper pump selection. When choosing a centrifugal pump, it is essential to accurately match the pump's performance curve with the actual system requirements. An oversized pump will operate inefficiently, consuming excessive energy. By conducting a detailed analysis of the required flow rate, head, and fluid properties, we can select a pump that operates at its optimal efficiency point. For example, in a water supply system, if the daily water demand varies, using a variable - speed pump can adjust the flow rate according to the actual need, rather than running a fixed - speed pump at full capacity all the time.
Another key aspect of energy - saving is maintaining the pump in good condition. Regular maintenance can prevent performance degradation and energy waste. This includes checking and replacing worn - out components such as impellers, seals, and bearings. A damaged impeller can disrupt the flow pattern inside the pump, increasing energy consumption. By replacing the impeller in a timely manner, we can restore the pump's efficiency. Additionally, proper lubrication of bearings is crucial as it reduces friction, which in turn lowers energy consumption.
Optimizing the pump system is also an effective energy - saving strategy. This involves minimizing the resistance in the pipeline system. For instance, reducing the number of unnecessary elbows, valves, and fittings in the pipeline can decrease the head loss. Smooth - walled pipes can also improve the flow characteristics and reduce energy losses. Moreover, proper sizing of the pipeline is important. If the pipeline is too small, it will cause excessive friction and energy consumption, while an overly large pipeline may lead to inefficient flow.
In some cases, implementing a control system can significantly contribute to energy savings. Variable - frequency drives (VFDs) are commonly used to adjust the speed of the pump motor. By controlling the motor speed according to the actual flow requirements, the pump can operate more efficiently. For example, in a cooling water system of a large industrial plant, when the cooling load decreases, the VFD can reduce the pump speed, saving a substantial amount of energy.
Furthermore, training the operating personnel is essential. Well - trained operators can better understand the pump's performance and operation principles. They can optimize the pump's operation by avoiding practices that waste energy, such as running the pump at non - optimal conditions for extended periods.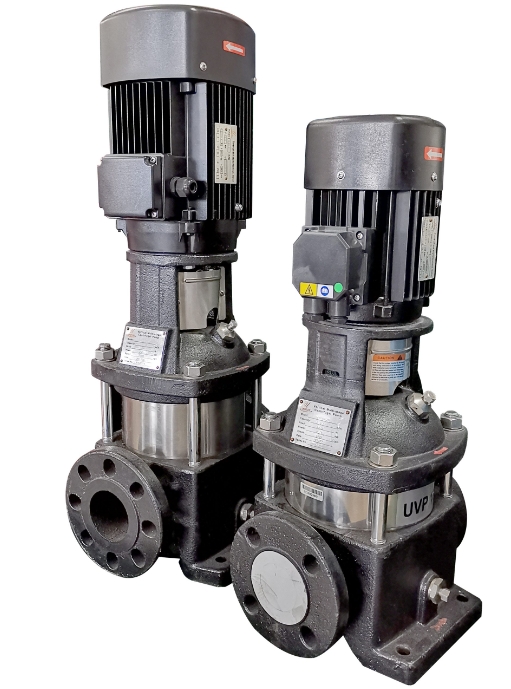
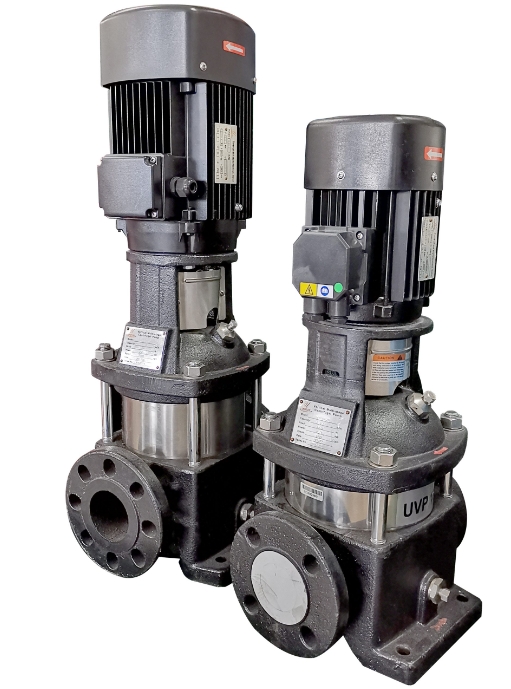
In conclusion, energy - saving in centrifugal pumps is a multi - faceted task. By carefully selecting the right pump, maintaining it properly, optimizing the system, implementing control systems, and training the operators, we can achieve significant energy savings. These energy - saving measures not only reduce the operating costs of enterprises but also contribute to environmental protection by reducing energy consumption and carbon emissions. It is crucial for all industries that rely on centrifugal pumps to continuously explore and implement these energy - saving methods to achieve sustainable development.
Get the latest price? We'll respond as soon as possible(within 12 hours)
more products
News
Featured Products
Contact Details