Introduction to Cavitation Phenomenon in Pumps
Introduction to Cavitation Phenomenon in Pumps
In the realm of fluid - handling machinery, cavitation is a significant and often - encountered phenomenon, especially in pumps. Understanding cavitation is crucial for ensuring the efficient, reliable, and long - lasting operation of pumps in various industrial applications.
Definition of Cavitation
Cavitation occurs when the pressure of the fluid within a pump drops below its vapor pressure at a given temperature. As the pressure decreases, the fluid begins to vaporize, forming small vapor bubbles or cavities. These bubbles are then carried along with the fluid flow. When they reach regions of higher pressure within the pump, they rapidly collapse. This process of bubble formation, growth, and subsequent collapse is what we refer to as cavitation.
Causes of Cavitation
One of the primary causes of cavitation is improper suction conditions. If the suction lift is too high, meaning the pump is trying to draw fluid from too great a depth, the pressure at the pump inlet can drop significantly. Additionally, a restricted or clogged suction line can impede the smooth flow of fluid into the pump, leading to a pressure drop. Another factor is the speed at which the pump is operating. Running a pump at an excessive speed can cause the fluid to accelerate rapidly, resulting in a pressure drop in certain areas of the pump impeller.
Harmful Effects of Cavitation
Cavitation can have several detrimental effects on pumps. Firstly, it causes severe damage to the pump components. The rapid collapse of the vapor bubbles generates high - intensity shockwaves. These shockwaves can erode the surfaces of the impeller, pump casing, and other internal parts. Over time, this erosion can lead to pitting, material loss, and eventually, the failure of the components. For example, in a water - pumping station, continuous cavitation can cause the impeller blades to become severely damaged within a relatively short period, necessitating costly replacements.
Secondly, cavitation reduces the efficiency of the pump. The presence of vapor bubbles disrupts the smooth flow of the fluid through the pump. Instead of a continuous and uniform flow, there are voids and disruptions, which lead to energy losses. As a result, the pump has to work harder to achieve the same level of fluid transportation, consuming more power and reducing overall efficiency.
Moreover, cavitation can also cause noise and vibration. The collapse of the bubbles produces distinct popping or crackling sounds, which can be an indication of cavitation occurring. The associated vibrations can affect the stability of the pump and the entire system, potentially leading to damage to other connected equipment.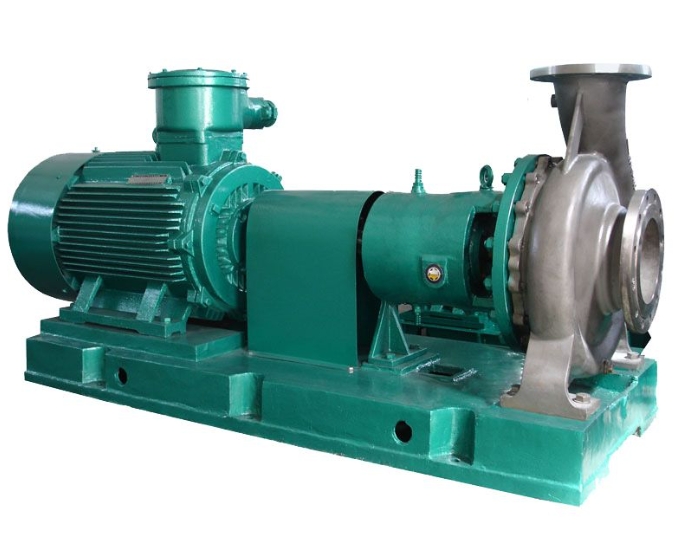
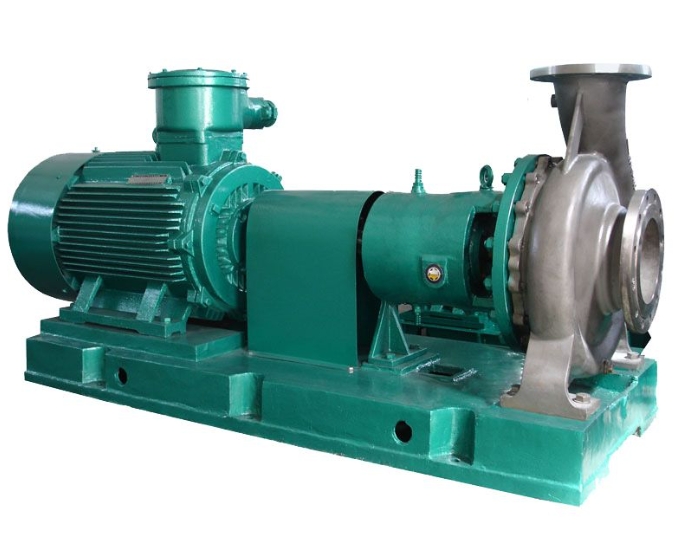
Prevention of Cavitation
To prevent cavitation, several measures can be taken. Ensuring proper suction conditions is of utmost importance. This includes maintaining an appropriate suction lift, keeping the suction line free from blockages, and using a properly sized suction pipe. Additionally, selecting the right pump for the application and operating it within its recommended speed range can help avoid cavitation. Installing a suction - side booster pump can also increase the pressure at the inlet of the main pump, preventing the pressure from dropping below the vapor pressure of the fluid.
In conclusion, cavitation is a complex and potentially damaging phenomenon in pumps. By understanding its causes, effects, and prevention methods, engineers and operators can take proactive steps to safeguard the performance and longevity of pumps, ensuring the smooth operation of fluid - handling systems.
Get the latest price? We'll respond as soon as possible(within 12 hours)
more products
News
Featured Products
Contact Details