Preventing Centrifugal Pump Motors from Burning Out
Preventing Centrifugal Pump Motors from Burning Out
Centrifugal pump motors are the workhorses of many industrial processes, powering the movement of fluids essential for operations. However, motor burnout is a common and costly issue that can disrupt production, lead to significant repair expenses, and cause downtime. In this post, we'll explore several effective strategies to safeguard centrifugal pump motors from burning out.
Overload Protection
One of the primary causes of motor burnout is overloading. When a centrifugal pump is forced to operate beyond its rated capacity, the motor has to work harder, drawing excessive current. Installing overload protection devices is crucial. Thermal overload relays, for example, monitor the motor's current. If the current exceeds a pre - set limit, the relay trips, cutting off the power supply to the motor. This prevents the motor from overheating due to prolonged overloading. Additionally, variable - frequency drives (VFDs) can be used not only to control the speed of the pump but also to protect against overload. VFDs can adjust the motor's speed and torque according to the actual load, ensuring that the motor operates within its safe limits.
Proper Cooling and Ventilation
Heat is the enemy of electric motors, and centrifugal pump motors are no exception. Adequate cooling is essential to prevent overheating. Motors are typically designed with ventilation systems, such as cooling fans and vents. Regularly cleaning these ventilation components is vital. Dust, dirt, and debris can accumulate over time, blocking the airflow and reducing the cooling efficiency. In industrial environments with high levels of particulate matter, installing air filters can help keep the ventilation system clean. For pumps operating in hot or humid conditions, additional cooling measures may be required, such as water - cooled jackets around the motor or using heat exchangers to dissipate the heat generated by the motor.
Insulation Maintenance
The insulation of the motor windings is critical for preventing electrical short - circuits, which can lead to motor burnout. Moisture, chemicals, and physical damage can degrade the insulation over time. To maintain the integrity of the insulation, motors should be protected from water ingress. In outdoor or wet environments, proper enclosures with waterproof seals should be used. Regularly inspecting the motor for any signs of insulation damage, such as cracks or discoloration, is also important. If any damage is detected, the affected parts should be repaired or replaced immediately. Additionally, using appropriate lubricants in the motor bearings can reduce friction and heat generation, which in turn helps protect the insulation.
Regular Maintenance and Monitoring
A comprehensive maintenance program is essential for the long - term health of centrifugal pump motors. This includes regular inspections of the motor's mechanical and electrical components. Checking the alignment of the pump and motor shafts, as misalignment can cause excessive vibration and stress on the motor. Monitoring the motor's performance parameters, such as current, voltage, and temperature, can provide early warnings of potential problems. Modern motor control systems often come with built - in monitoring capabilities, allowing operators to track the motor's condition in real - time. By analyzing this data, maintenance teams can identify trends and take proactive measures to prevent motor burnout.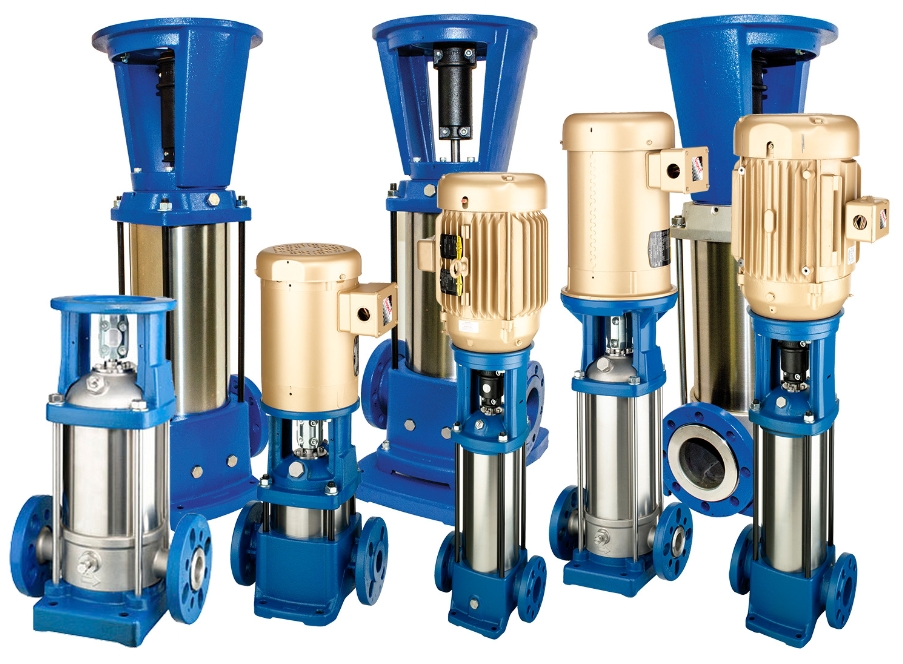
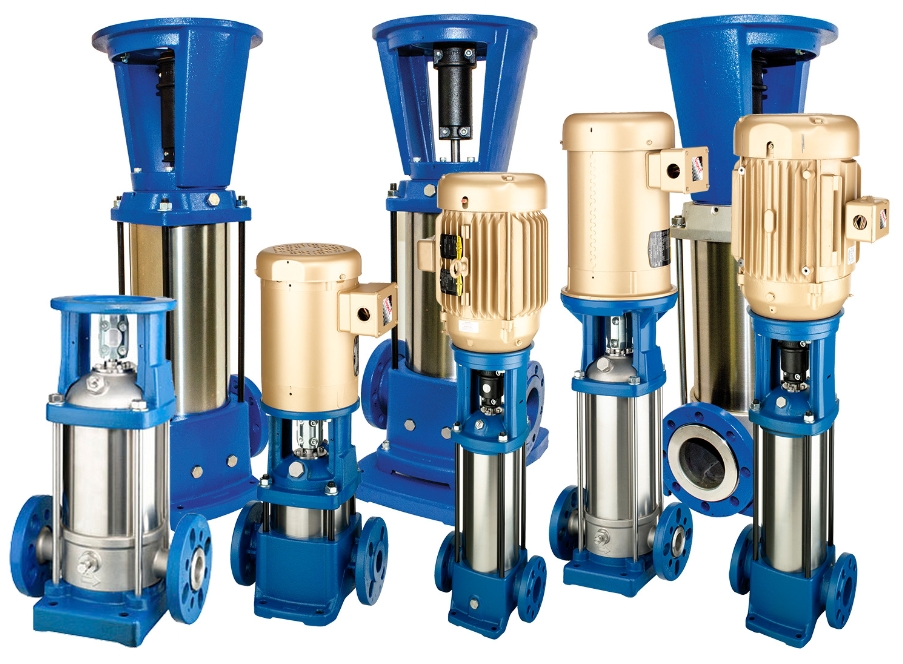
In conclusion, preventing centrifugal pump motors from burning out requires a multi - faceted approach. By implementing overload protection, ensuring proper cooling and ventilation, maintaining insulation, and conducting regular maintenance and monitoring, we can significantly extend the lifespan of these motors, reduce the risk of costly breakdowns, and ensure the smooth operation of industrial processes.
Get the latest price? We'll respond as soon as possible(within 12 hours)
more products
News
Featured Products
Contact Details