The Influence of Power Loss on the Performance of Centrifugal Pumps
The Influence of Power Loss on the Performance of Centrifugal Pumps
Centrifugal pumps are widely used in various industrial fields, such as water supply and drainage systems, chemical processes, and power generation plants, due to their simple structure, high efficiency, and stable operation. Power loss is an important factor that significantly affects the performance of centrifugal pumps. Understanding this influence is crucial for optimizing pump operation, improving energy efficiency, and reducing operational costs.
1. Types of Power Loss in Centrifugal Pumps
1.1 Mechanical Loss
Mechanical loss mainly occurs in the mechanical components of the pump. One of the main sources is the friction between the pump shaft and the bearings. As the shaft rotates at high speeds, continuous contact with the bearings generates frictional heat and energy dissipation. Additionally, the packing or mechanical seals used to prevent leakage also contribute to mechanical loss. For example, in a large - scale industrial centrifugal pump with a long - running time, the wear of the packing seal can gradually increase the frictional resistance, leading to a higher mechanical power consumption.
1.2 Hydraulic Loss
Hydraulic loss is related to the flow of fluid within the pump. When the liquid flows through the impeller, volute, and other flow - passage components, it encounters resistance. This resistance is caused by factors such as the roughness of the inner surface of the flow - passage, sudden changes in the cross - sectional area, and flow separation. For instance, if the inner surface of the pump casing is not smooth enough due to corrosion or scaling, the hydraulic loss will increase, and more energy will be consumed to overcome this resistance during the fluid flow process.
1.3 Leakage Loss
Leakage loss occurs when there is an unwanted flow of fluid within the pump. This can happen between the impeller and the pump casing, or through the seals. In a centrifugal pump, a small amount of liquid may leak from the high - pressure side to the low - pressure side. This leakage not only reduces the effective flow rate of the pump but also requires additional energy to maintain the pressure difference. For example, in a multistage centrifugal pump, if the inter - stage seals are not well - maintained, significant leakage can occur, resulting in a waste of energy.
2. Influence on Pump Performance
2.1 Flow Rate
Power loss has a direct impact on the flow rate of a centrifugal pump. As power loss increases, the available power for fluid transportation decreases. According to the pump's performance curve, a reduction in power leads to a decrease in the flow rate that the pump can deliver. For example, if a centrifugal pump originally has a designed flow rate of 100 cubic meters per hour, but due to increased mechanical and hydraulic losses, the available power drops, the actual flow rate may be reduced to 80 cubic meters per hour. This reduction in flow rate can disrupt the normal operation of the entire system, such as in a water - supply network where insufficient water flow may affect the water supply to users.
2.2 Head
The head of a centrifugal pump, which represents the height or pressure that the pump can lift the fluid, is also affected by power loss. Higher power losses mean that more energy is consumed within the pump itself, leaving less energy to increase the pressure of the fluid. As a result, the pump's head - generating capacity decreases. In a pumping system for a high - rise building, if the centrifugal pump experiences significant power loss, it may not be able to provide sufficient head to supply water to the upper floors, causing water - supply problems.
2.3 Efficiency
Efficiency is a key performance indicator of a centrifugal pump, and power loss is a major factor that reduces it. The efficiency of a centrifugal pump is calculated as the ratio of the useful power output (hydraulic power) to the input power. When power losses such as mechanical, hydraulic, and leakage losses increase, the input power needs to be increased to maintain the same hydraulic power output. This results in a lower efficiency value. For example, a well - maintained centrifugal pump may have an efficiency of 80%, but as power losses accumulate over time, the efficiency may drop to 60% or even lower. A decrease in efficiency not only means higher energy consumption but also higher operating costs for the entire system.
3. Strategies to Reduce Power Loss
3.1 Regular Maintenance
Regular maintenance of centrifugal pumps is essential to reduce power loss. This includes checking and replacing worn - out bearings, ensuring proper lubrication, and maintaining the integrity of the seals. By keeping the mechanical components in good condition, mechanical losses can be minimized. For example, replacing old and worn - out packing seals with new ones can reduce frictional resistance and thus mechanical power consumption.
3.2 Flow - Passage Optimization
Optimizing the design of the flow - passage components can significantly reduce hydraulic losses. This can involve using smooth - surface materials for the pump casing and impeller, and improving the shape of the flow - passage to reduce flow separation and sudden changes in cross - sectional area. For instance, modern centrifugal pumps often use advanced manufacturing techniques to produce impellers with precise geometries, which can improve the flow characteristics of the fluid and reduce hydraulic losses.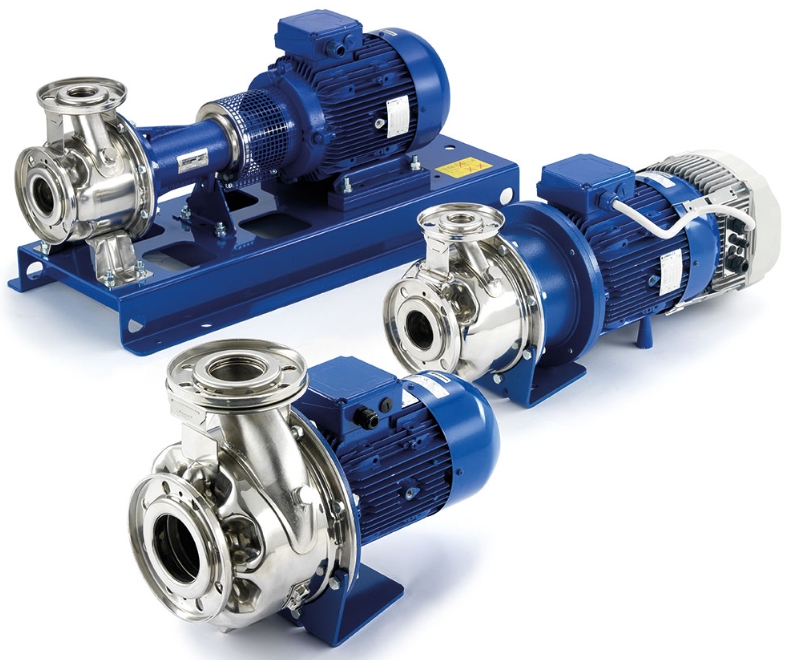
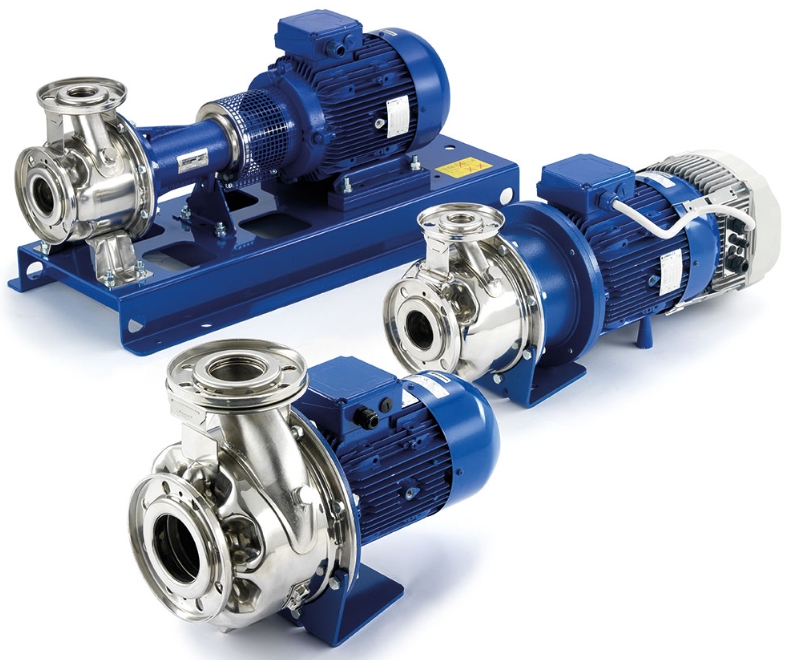
3.3 Leakage Prevention
To prevent leakage loss, proper installation and maintenance of seals are crucial. Regularly inspecting the seals and replacing them when necessary can effectively reduce the amount of fluid leakage within the pump. In addition, using high - quality seals and ensuring proper sealing design can also help to minimize leakage loss.
In conclusion, power loss has a profound impact on the performance of centrifugal pumps, affecting parameters such as flow rate, head, and efficiency. By understanding the types of power loss and taking appropriate measures to reduce them, the performance of centrifugal pumps can be optimized, leading to more efficient and cost - effective operation in various industrial applications.