Analyzing Screw Pump Flow Rate and Its Significance in Industrial Applications
Analyzing Screw Pump Flow Rate and Its Significance in Industrial Applications
In industrial settings, screw pumps are widely used for fluid transfer due to their ability to handle a variety of fluids, from low - viscosity liquids to highly viscous substances. One of the most crucial aspects of evaluating a screw pump's performance is analyzing its flow rate.
Let's consider a real - world example in the beverage industry. A large - scale brewery was using a screw pump to transfer a mixture of water, malt, and hops during the brewing process. The pump was designed to have a flow rate of 30 cubic meters per hour. However, during production, the operators noticed that the actual flow rate was only around 20 cubic meters per hour, which led to a slowdown in the brewing process and potential production losses.
The first step in analyzing this flow - rate issue is to check the pump's rotational speed. As we know, for a screw pump, the flow rate is directly proportional to the rotational speed. Using a tachometer, the maintenance team measured the speed of the pump's drive shaft. They found that the actual speed was lower than the rated speed. After further investigation, it was discovered that the motor driving the pump had a problem with its frequency converter. The frequency converter was set to a lower frequency than required, which reduced the motor's speed and consequently the pump's flow rate. Once the frequency converter was adjusted to the correct settings, the motor speed increased, and the pump's flow rate returned closer to the rated value.
Another factor that can affect the flow rate of a screw pump is the condition of its internal components. In the brewery's case, after running for a long time, the screws inside the pump had experienced some wear. The wear increased the clearances between the screws and the pump casing. When the clearances are larger, more fluid leaks back internally within the pump, reducing the amount of fluid that is actually discharged. To solve this problem, the brewery had to replace the worn - out screws with new ones. After the replacement, the internal leakage was minimized, and the flow rate improved significantly.
This example shows that when analyzing the flow rate of a screw pump, we need to consider both the external factors like the drive system and the internal factors related to the pump's components. Regular monitoring of these aspects can help industries avoid production disruptions caused by abnormal flow rates.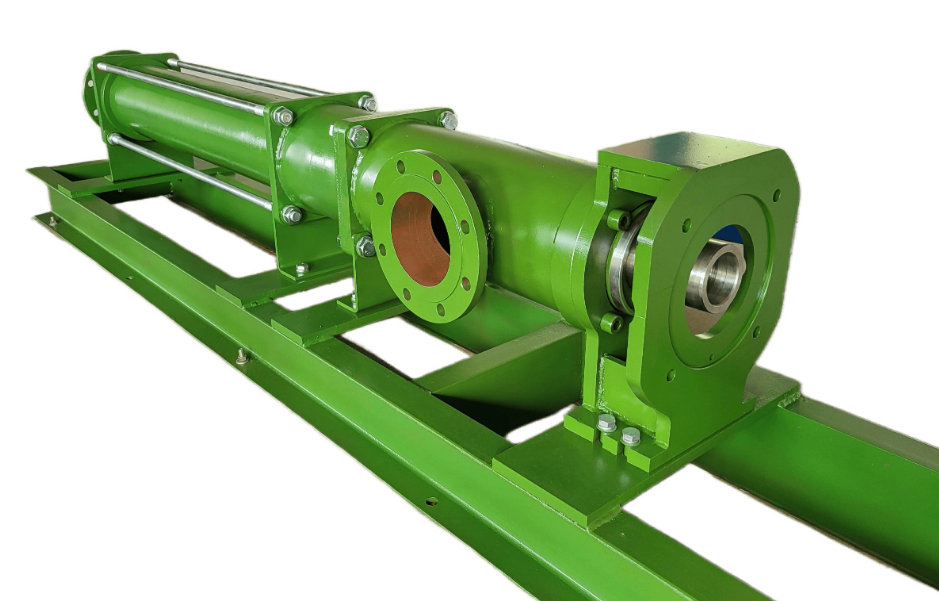
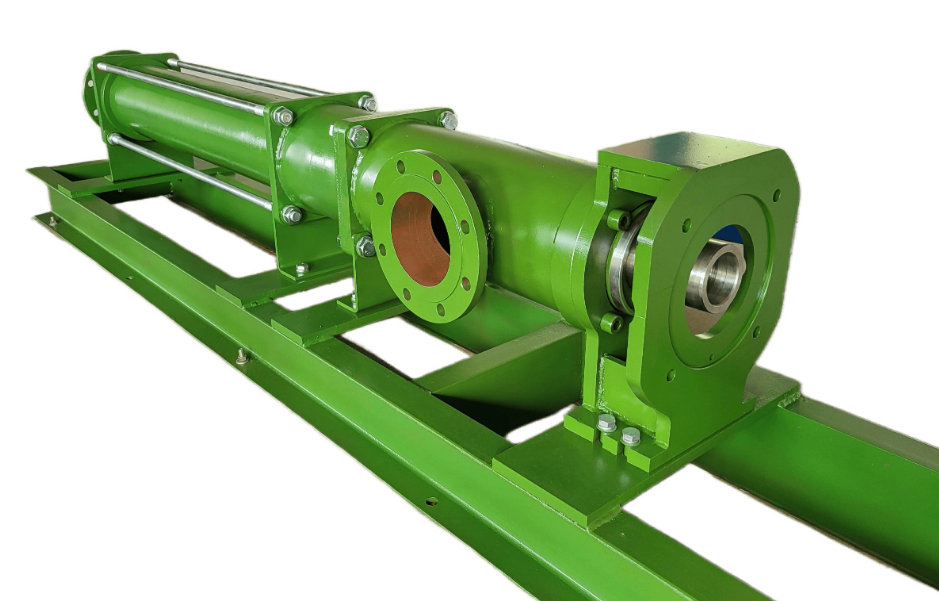
Get the latest price? We'll respond as soon as possible(within 12 hours)
more products
News
Featured Products
Contact Details